Our Other Supply Chain Services
Minimising inventory
Inventory is the sum of all your products stored and can include finished products, raw materials, work in progress, returns, promotional materials, etc. depending on your business, but it is built up by decisions made at individual product level by the person responsible for the product.
This person might be a factory or warehouse manager, but it is more frequently the buyer or merchandiser for the product or product group.
Your starting point for minimising inventory is to identify the drivers behind the quantity you have to stock. These could include long lead times, minimum batches or order quantities, popularity, promotional activity, seasonality etc.
LPC - helping you to optimise your inventory and storage
At LPC we frequently find with our customers that the responsibility is fragmented across a number of people and that the amount and value of inventory increases over time and that an inventory review will result in the identification of opportunities to reduce the stockholding.
In some instances there is the need to restrict stockholding on a particular site due to space constraints or to centralise or decentralise. Whatever the challenge LPC can help you to optimise your inventory and storage.
Inventory management
Inventory management is an ongoing process vital to the health and efficiency of your storage operation. No business is entirely static and products have lifecycles with their profile changing over time. A product might be initially be a fast mover when newly introduced with sales falling over time as newer products are introduced, or it might be seasonal, or have other characteristics. Inventory management should take account of these changes and proactively make changes such as location changing as popularity changes, or reducing ordering towards the end of the season to avoid being left with last season’s stock.
The focus of inventory management is rightly on the saleable stock, but some of the other areas can have a significant impact on a warehouse operation and should not be forgotten. These include packaging, consumables and non-sales items used in the operation, point of sale, marketing and promotional materials, records, aged or damaged stock, returns from customers and returns going to suppliers.
At LPC we take a holistic approach to inventory that considers everything held and its requirements and impact. Inventory is a key component of your operation and can’t be considered in isolation.
Product Grouping And Segmentation
A product in storage needs a location. The location could be chosen at random, but it is much better for your operation to have a location strategy and rules to determine the location of each product to drive up your productivity and optimise your storage footprint and improve space efficiency. The strategy and rules you need will be based on product grouping and segmentation.
Considering product groups; if you can identify some products that can be grouped together based on size and properties or commonalities and compatibilities you have the opportunity to design your racking and shelving to suit the physical characteristics of a particular group and minimise wasted space, improve the presentation to the picker to make it easier for them to access the product.
Products that are ordered together can be co-located to minimise walking time and improve productivity.
Segmenting your products can also be undertaken by popularity with the range split into fast, medium and slow movers. The faster movers could then be located nearer to your packing or despatch areas with medium and slower movers further away. This will reduce your overall travel distances, increase the proportion of your pickers time spent on picking and improve your productivity.
LPC have considerable experience in reviewing inventory, product categories and segmentation to identify the optimal location strategy to drive your operation forward and improve your efficiency.
Space Utilisation And Product Management
Space itself is costly – rent rates, utilities, maintenance etc. The lack of space can be costlier still if you have to outsource storage or acquire other facilities. However poor utilisation of existing space can also increase your operational costs and impact the operation of your business. Optimising your space utilisation can therefore pay dividends.
The correct locations sizes, optimum aisle widths for the MHE and levels of activity, use of the height and the cube of your facility as well the footprint will all help, but for the best results they need to be allied with product management. Product management in the warehouse is best carried out by choosing the right products in appropriately sized picking locations in the correct place, grouping products to suit their properties and order profiles. Creating the correct set up from the start and then the ongoing management as products and demand changes through seasonality / lifecycle will provide long term benefits to your operation.
LPC has extensive expertise to help you optimise your space utilisation and product management to consolidate your operation or get more out of your existing operation in the most efficient manner possible.
JIT Deliveries Push Stock Back Up The Supply Chain
You need to have products available for your customers, but do you need to stock all the products, or do you need to stock so much. Just in time deliveries are all about taking advantages of the capabilities of your suppliers to meet your service proposition to your customers. If you can move some products / suppliers onto a JIT basis and receive, sort and cross-dock some products you will reduce your costs and storage space required. You will also reduce the capital you have tied up in stock.
JIT deliveries will probably need to be sorted into orders for despatch and have to be integrated with other products that you have stocked. Your warehouse layout and processes will probably need some changes and your IT systems will need to be aligned. The operation has to be slick because it is typically more time dependent than traditional warehousing. LPC can help you with any changes and determine the functionality required from your IT systems to support a JIT operation.
Book a FREE Healthcheck
Read Our Blog
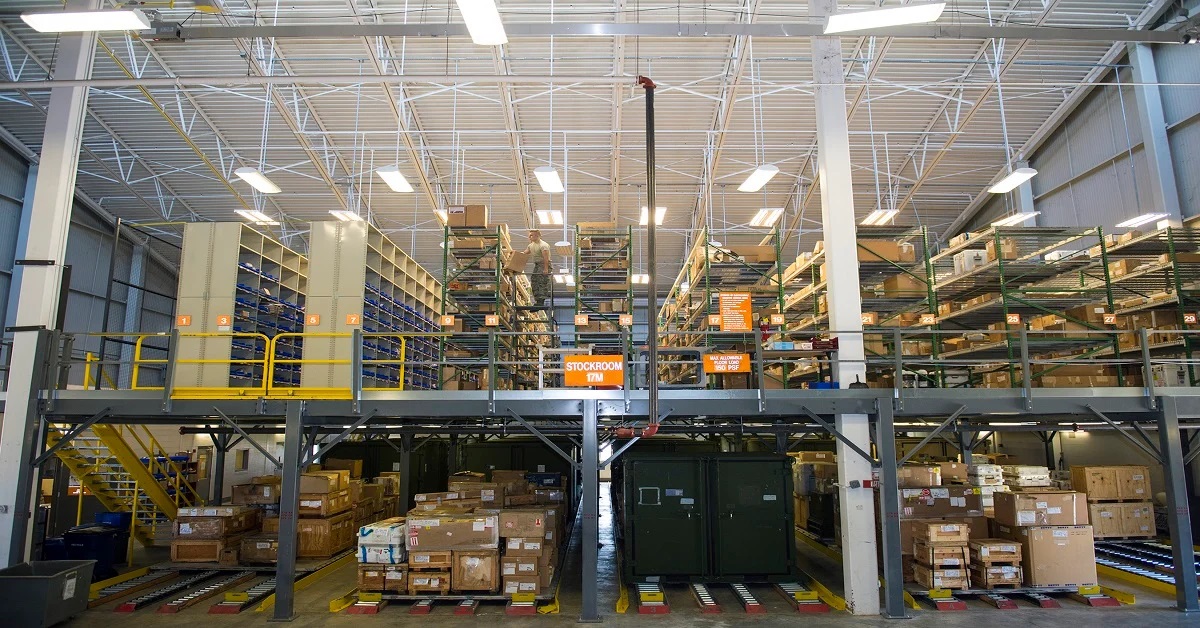
Understanding Supply Chain Management
Supply chain management is often confused with logistics, which is only one component of the supply chain, albeit a significant one.
Your supply chain is every touchpoint for a product that is delivered to a customer. It starts with suppliers of materials, components or services right through to eventual outbound delivery and customer service. It needs a strategy to control and optimise because it accounts for the majority of costs in many businesses.
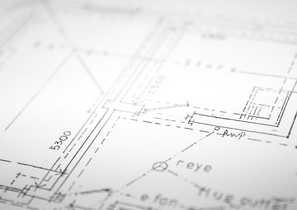
Why You Need A Dedicated WMS – Not Just An ERP
Enterprise Resource Planning (ERP) software is often regarded as a one-stop solution for businesses seeking to streamline their core processes, improve interdepartmental collaboration, and reduce costs.
A well-designed ERP platform will often feature warehouse management, or more likely basic stock keeping capabilities, but it is important to understand that a dedicated Warehouse Management System (WMS) delivers greater functionality …
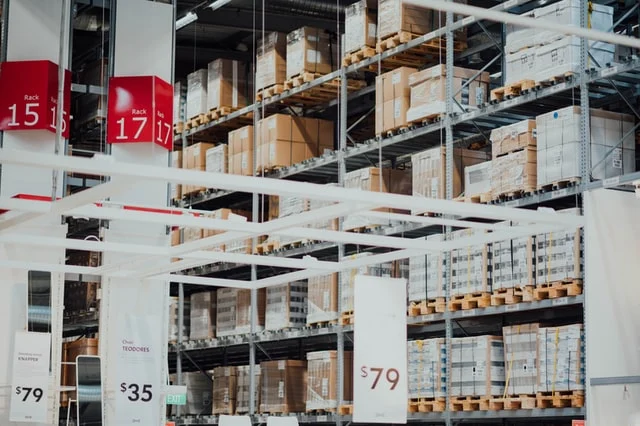
Better Warehouse Management – Where To Start
Warehouse management is a vital component of any successful business. It’s critical to keep your warehouse and logistics operations running smoothly so you can deliver correctly, on time, every time, and to organise your stock, workforce, and assets in the most productive and cost-effective way. Many areas of the warehouse benefit from continuous improvement, including your staffing strategy, relationships with third parties, your software systems, automation technologies, and the layout of the warehouse itself.